Advanced technology in plastic extrusion for current industries
Advanced technology in plastic extrusion for current industries
Blog Article
A Comprehensive Guide to the Process and Advantages of Plastic Extrusion
In the huge world of production, plastic extrusion arises as a vital and extremely reliable procedure. Altering raw plastic into continual accounts, it provides to a plethora of sectors with its amazing flexibility.
Understanding the Basics of Plastic Extrusion
While it might show up complex at first glimpse, the procedure of plastic extrusion is basically straightforward. The procedure begins with the feeding of plastic product, in the form of pellets, powders, or granules, into a warmed barrel. The designed plastic is then cooled, solidified, and reduced into wanted sizes, finishing the procedure.
The Technical Refine of Plastic Extrusion Explained
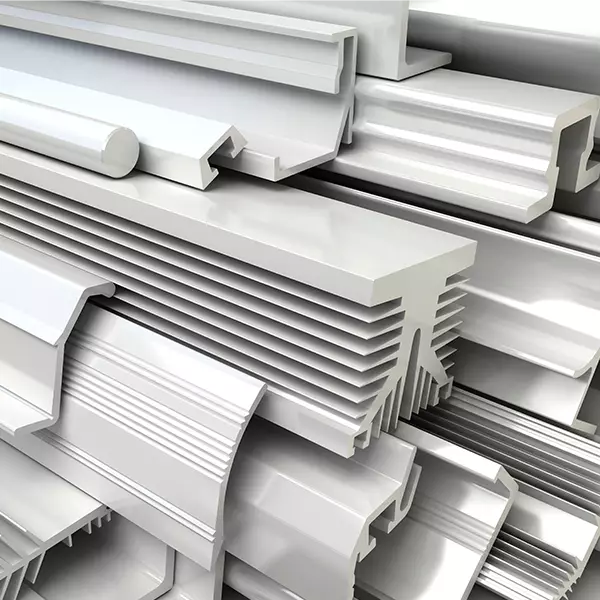
Sorts Of Plastic Suitable for Extrusion
The option of the appropriate sort of plastic is an important facet of the extrusion procedure. Various plastics use one-of-a-kind properties, making them more fit to specific applications. Polyethylene, for instance, is commonly used because of its reduced price and simple formability. It provides exceptional resistance to chemicals and dampness, making it perfect for items like tubing and containers. Similarly, polypropylene is one more popular selection due to its high melting point and resistance to exhaustion. For more durable applications, polystyrene and PVC (polyvinyl chloride) are frequently chosen for their strength and resilience. These are common choices, the selection ultimately depends on the specific demands of the product being produced. Comprehending these plastic types can substantially improve the extrusion procedure.
Contrasting Plastic Extrusion to Other Plastic Forming Approaches
Understanding the sorts of plastic ideal for extrusion leads the way for a more comprehensive discussion on exactly how plastic extrusion piles up against other plastic developing approaches. These include shot molding, impact molding, and thermoforming. Each approach has its special uses and benefits. Injection molding, for example, is exceptional for creating elaborate parts, while strike molding is perfect for hollow objects like containers. Thermoforming excels at developing large or superficial parts. Nevertheless, plastic extrusion is unmatched when it pertains to creating continuous profiles, such as pipes, seals, and gaskets. It additionally permits for a constant cross-section along the size of the product. Hence, the option of approach largely depends upon the end-product demands and requirements.
Key Benefits of Plastic Extrusion in Manufacturing
In the world of manufacturing, plastic extrusion provides lots of considerable advantages. One notable benefit is the cost-effectiveness of the process, which makes it a financially appealing manufacturing approach. Additionally, this method supplies superior product adaptability and boosted production speed, thus boosting general manufacturing performance.
Cost-Effective Production Technique
Plastic extrusion jumps to the center as an affordable manufacturing technique in production. This More Bonuses process sticks out for its ability to generate high volumes of product promptly and successfully, providing producers with significant cost savings. The Click Here primary expense advantage is the capacity to utilize much less pricey resources. Extrusion utilizes thermoplastic products, which are much less costly compared to metals or ceramics. Additionally, the extrusion procedure itself is relatively easy, minimizing labor expenses. Additionally, plastic extrusion calls for much less energy than traditional manufacturing techniques, adding to lower operational expenses. The process likewise minimizes waste, as any type of excess or defective materials can be reused and reused, offering one more layer of cost-effectiveness. Generally, the economic benefits make plastic extrusion an extremely appealing alternative in the manufacturing industry.

Superior Item Adaptability
Beyond the cost-effectiveness of plastic extrusion, an additional substantial benefit in manufacturing lies in its premium item adaptability. This makes plastic extrusion an ideal solution for industries that call for personalized plastic parts, such as automobile, building and construction, and packaging. In essence, plastic extrusion's item flexibility cultivates innovation while improving operational efficiency.
Improved Manufacturing Speed
A significant benefit of plastic extrusion lies in its improved production speed. Couple of other production procedures can match the rate of plastic extrusion. Additionally, the capacity to keep constant high-speed production without compromising product high quality establishes plastic extrusion apart from various other approaches.
Real-world Applications and Impacts of Plastic Extrusion
In the realm of production, the strategy of plastic extrusion holds extensive significance. This process is widely utilized in the click manufacturing of a range of items, such as plastic tubes, window frames, and weather condition removing. Consequently, it greatly influences industries like building and construction, product packaging, and automotive sectors. Its impact expands to daily products, from plastic bags to tooth brushes and disposable flatware. The financial advantage of plastic extrusion, primarily its cost-effective and high-volume outcome, has transformed manufacturing. The environmental effect of plastic waste continues to be a problem. The market is persistently making every effort for technologies in recyclable and naturally degradable products, showing a future where the advantages of plastic extrusion can be kept without endangering ecological sustainability.
Verdict
To conclude, plastic extrusion is a effective and highly effective method of transforming basic materials into varied items. It uses many benefits over various other plastic forming approaches, including cost-effectiveness, high output, marginal waste, and layout adaptability. Its impact is greatly felt in different industries such as building, automotive, and durable goods, making it a crucial procedure in today's manufacturing landscape.
Digging deeper right into the technological process of plastic extrusion, it begins with the choice of the proper plastic material. Once cooled, the plastic is reduced right into the required sizes or wound onto reels if the item is a plastic film or sheet - plastic extrusion. Contrasting Plastic Extrusion to Various Other Plastic Forming Approaches
Recognizing the kinds of plastic ideal for extrusion leads the method for a more comprehensive discussion on how plastic extrusion stacks up versus various other plastic developing approaches. Couple of other production processes can match the speed of plastic extrusion.
Report this page